Mastering the Art of Bolts and Machining: Developments and Finest Practices
In the world of commercial production and engineering, the mastery of bolts and machining is a foundation of making sure architectural honesty, performance, and long life in different applications. Join us as we check out the latest developments and delve right into the nuanced world of understanding fasteners and machining, revealing essential insights and strategies that can elevate your approach to design remedies.
Evolution of Fastening Technologies
Throughout the commercial revolution and into the modern age, the evolution of fastening innovations has been noted by continuous advancements in effectiveness and integrity. Bolts, such as rivets, screws, and bolts, play a crucial role in different industries, consisting of auto, aerospace, construction, and electronics. The requirement for stronger, extra durable, and easier-to-install attachment options has actually driven development in the area.
One considerable development has been the shift in the direction of precision machining methods to develop bolts with greater tolerances and exceptional efficiency. This change has made it possible for suppliers to create bolts that fulfill stringent quality criteria and deal boosted resistance to corrosion and fatigue.
In addition, the introduction of advanced materials, such as titanium alloys and compounds, has actually reinvented the capacities of fasteners. Fasteners and Machining. These materials give extraordinary strength-to-weight ratios, making them perfect for applications where lowering weight is vital without jeopardizing architectural stability
Advancements in Machining Approaches
In the realm of industrial production, the continuous development of machining methods has actually led the way for unprecedented accuracy and performance in the manufacturing of bolts. One of the significant developments in machining approaches is the application of Computer system Numerical Control (CNC) modern technology. CNC devices provide unparalleled accuracy and repeatability by allowing for automated control of machining devices. This exact control allows producers to develop complex and detailed fastener styles easily.

In addition, the fostering of multi-axis machining centers has allowed simultaneous reducing operations from various angles, even more enhancing effectiveness and reducing manufacturing times. By utilizing these go right here advanced machining methods, producers can meet the raising demand for top quality bolts while preserving cost-effectiveness in their procedures.
Picking the Right Bolt Products
Picking the proper material for fasteners is an essential decision see here that significantly impacts the performance and durability of the put together elements. When selecting the best bolt material, numerous factors should be considered to ensure the toughness and dependability of the final product. The material chosen must be compatible with the environmental conditions the fasteners will be revealed to, such as temperature variants, dampness degrees, and corrosive components.
Common materials utilized for fasteners consist of stainless steel, carbon steel, light weight aluminum, and titanium, each offering distinct residential or commercial properties that fit different applications. Carbon steel is a cost-efficient option suitable for lots of general-purpose applications.
Enhancing Precision in Machining
Attaining ideal accuracy in machining is essential for guaranteeing the top quality and efficiency of machined components. To improve precision in machining, suppliers utilize a variety of innovative strategies and innovations.
In enhancement to CNC machining, the use of innovative cutting devices and tool owners can likewise considerably enhance precision. By prioritizing precision in machining, manufacturers can attain superior product you can try this out quality, tighter tolerances, and boosted total efficiency of machined elements.
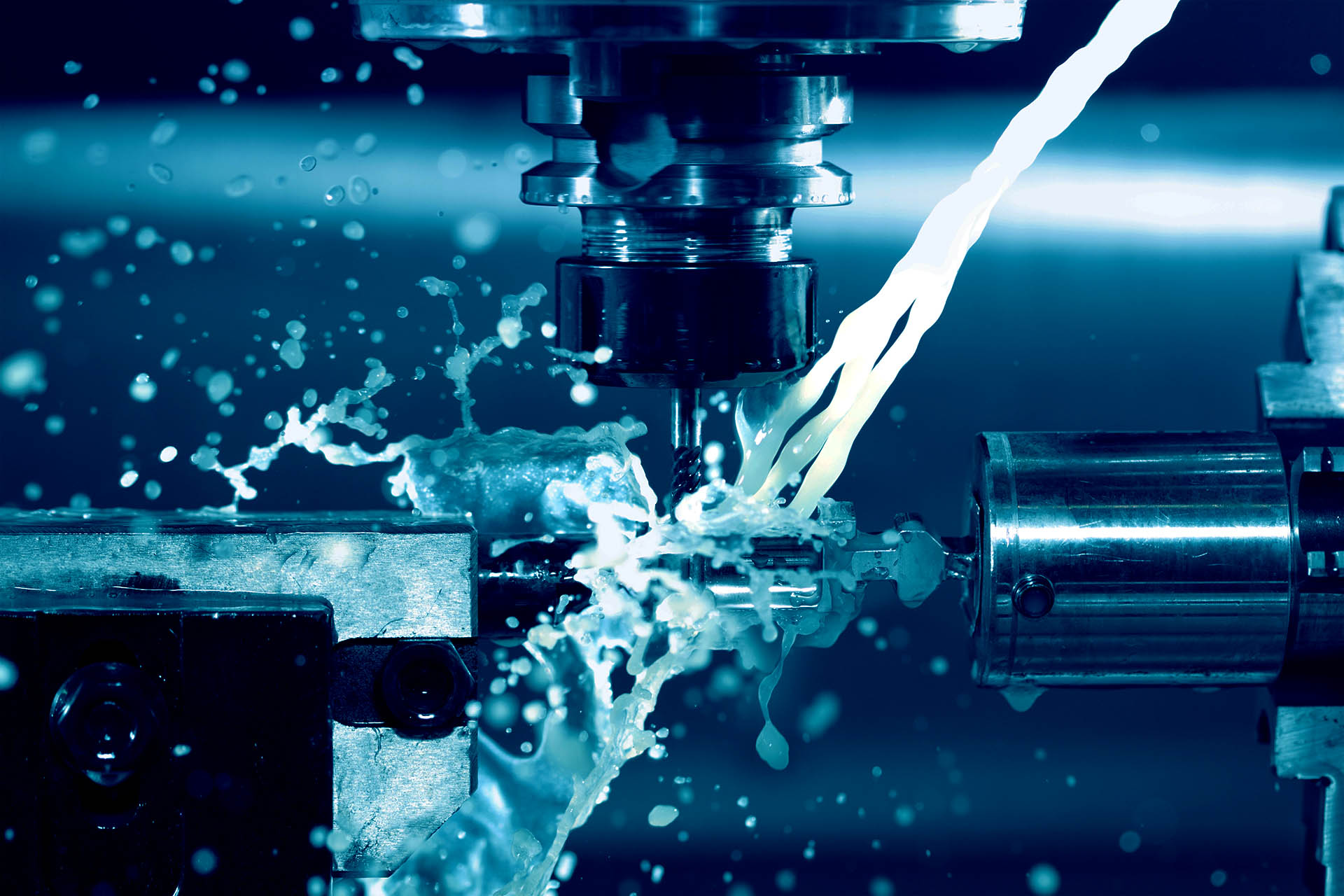
Best Practices for Fastener Installment
Precision in machining plays an important duty in making sure the reliability and durability of bolt installations. When it comes to best practices for fastener setup, one crucial element is the correct option of bolts based upon the particular application requirements. Utilizing the right type, dimension, and material of bolt is necessary to assure ideal performance and longevity. Fasteners and Machining. In addition, it is vital to adhere to supplier guidelines and recommended torque worths throughout the installation process to stop over-tightening or under-tightening, which can lead to premature bolt failure.
Additionally, making sure that the fastener strings are tidy and cost-free of debris prior to setup is crucial to attaining a secure and effective link. By sticking to these finest practices, manufacturers can optimize the honesty and performance of their bolt installments.
Verdict
By picking the ideal fastener materials and enhancing precision in machining, suppliers can accomplish optimal results in their operations. Generally, grasping the art of bolts and machining includes continual innovation and adherence to ideal methods.
In the world of commercial production, the continuous development of machining approaches has actually led the method for unprecedented precision and performance in the manufacturing of fasteners.Precision in machining plays a critical function in making certain the dependability and long life of fastener installments. When it comes to finest techniques for fastener installation, one essential facet is the proper option of bolts based on the particular application requirements. By choosing the right bolt products and improving precision in machining, makers can accomplish optimum outcomes in their operations. Overall, understanding the art of fasteners and machining entails constant development and adherence to best practices.